Automation Platform and OnPing Scalability: Interview
The influence of Automation is rapidly expanding through the industrial environment. As industry changes, tools are quickly developed and discarded to keep up with industry standards of performance. The breakneck pace of development in Industrial Automation can be overwhelming for those testing the waters of Automation for the first time and industry experts alike leaving people to questions of: How do we start Automating our facilities? How do we manage costs? What happens when it’s time to grow? We sat down with an OnPing product manager for an interview to give his thoughts about Automation, OnPing as an Industrial Automation Platform, and some of the questions he’s heard before.
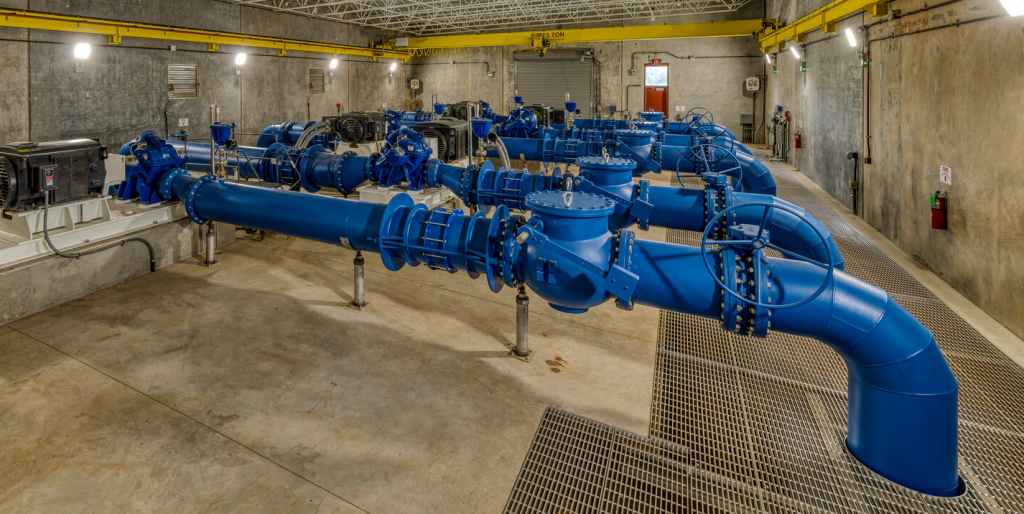

Weāve spoken a lot recently about what OnPing is. Much of that discussion has been focused on OnPing as an Industrial Automation Platform. So first, what is Automation to you?
Well, thatās a good question. Obviously, automation is simply a thing that happens with limited interaction. But when you talk about Industrial Automation, you have to think about what it means for something to happen with limited human interaction over the course of time. When you think about that, you realize that Automation is the process of making a machine do precisely what you want it to do, when you want to do it – reliably. And thatās quite a difficult challenge.
What are the benefits in taking on this challenge?
Automation is an idea that people intrinsically understand as beneficial. You have something that you used to pay a person to do, and now you donāt have to pay a person to do it. Thatās great. It means that a person can go do something else or you can run with less people – there are just all sorts of things that are nice about that.
But when you meet grizzled industrial veterans and start to talk about Automating something they will sort of scoff at you. That attitude is coming from, āSure, you made it where someone doesnāt have to touch the machine that weighs the flour – youāve automated weighing the flour. But what you havenāt automated is the 37 problems Automation has created.ā
To get the machine that weighs the flour to work reliably in this automated fashion you now need 3 other people involved. It can become questionable then what kind of return on investment you are getting. This is a real concern.
Thatās what the challenge of Automation is – Automating a process while ensuring maintenance of that process remains inexpensive.
Considering this, should you Automate every process in your business?
Iād like to think people are making those evaluations, because they are really important to consider, but itās a complicated question to answer.
In modern industry, youāll hear a lot of people talk about industry 4.0 and modern industry practices – theyāre collecting savings by harvesting easy wins. They find processes that you can show a direct benefit. But what is unclear is whether that project work to create benefits ends up costing more or less, especially when you consider how many automation projects and initiatives end up failing or donāt end up being the ārightā idea for the company.
When Industrial companies are considering Automation, they need to find a place to dip their toes in. This is something the software world figured out a long time ago. Software companies find a way to prove out an idea as cheaply as possible instead of launching giant initiatives. However, because of how funding works in industry, you see huge projects with drastic capital outlays for unproven ideas. It would be much better to find a small proof-of-concept you can use to build out and turn into a well Automated and process while learning lessons along the way.
Water Treatment plants have been an internal focus for us. What is a small place they could dip their toes into?
Thatās a nice example. First, water treatment is well understood. In commercial industry this isnāt the case, but in water treatment there are a lot of pieces that make sense.
Your inflows and outflows would be an obvious first step. If you know how much water is coming in and how much water is going out, that tells you a lot about what is going on in the plant. Same thing for turbidity.
These are data points that can give a lot of information regarding how well the water treatment center is operating.
Automation then, is about starting with a building block and working up from there.
Yeah, absolutely. Water Treatment is especially nice in that way. You can build out from one process and end up Automating everything in increments.
OnPing is an Industrial Automation Platform. How do you make the distinction between platform and Automation services?
There are many tasks integral to Automation. One is data collection ā think traditional SCADA pieces. SCADA is where OnPing got our start and we still have a fully capable SCADA system. You definitely need SCADA as a feature, but itās not enough.
In a modern Automation environment, you want a way to enable experimentation. You want a way to add in a few data points and monitor a new statistic without requiring a robust understanding of the full system.
Maybe you want to connect two warehouses together to share data, but they are located at opposite ends of the state: With traditional systems this requires finding a new tool developed for that purpose.
The idea of an Automation Platform is to bring all the pieces of Industrial Automation into one tool. This includes all the traditional SCADA tools such as reporting, visualization, and HMI, but it also includes tools like Simplified Networking, Site-to-Site scripting, VPN Deployment, Low-Code Dashboard Management, Cloud Back-Ups, and other features that allow you to work on these projects and make them grow as you find successful ways to implement the Automation. And thatās the key: With a platform you can start out small using just the parts you need.
Scalability and Ease of Use are key concepts in industry. What does Scalability mean to you, and what does it look like for someone to start small and grow their Automation footprint on the OnPing Industrial Automation Platform?
There are a bunch of businesses and industries that would benefit from more data and control integration into their products, but itās really hard to make that fit into a price point or business model. Companies can be cash-tight. So they need just exactly what is necessary to enable that product to have a more rich user experience.
A really good example of this is when companies are building things like mobile skids or you know, OEM equipment thatās going to sit on a factory floor. They might want to give their customers access to additional pieces of data and additional control points, but currently that means hiring a software developer, maybe an industrial applications engineer, pulling all that data into some device, standing up some kind of cloud system, pushing that data there, etc.
OnPing allows you to just pull in the data from your machine and use OnPing as a platform to serve all of that stuff for your customers. We call that platforming a product and we have a couple of different partners that have platformed their products within OnPing.
So what do you get? By default you have a system that will scale. You start out selling 10-20 pumps, then suddenly youāre selling a thousand pumps – our infrastructure will scale right along with you. There is no extra investment into software development to keep up with that.
Also, you get cloud back-ups, continuous over the year updates, a system that will work in both high security environments and locations more considered remote telemetry – all those answers are baked into the platform.
So what are you thinking as a business owner? Youāre thinking about the best ways to present data, what are the most useful pieces of information for my customers, instead of worrying about the best protocol to send data to a cloud server. We move the burden off all that extra stuff to the platform so you can just do what you need to do.
The OnPing Industrial Automation Platform is customizable – how does that relate to overall Ease of Use for users?
I like to think about Android vs IOS as the most relatable analogy. Generally speaking, iPhoneās are intuitive to use when first getting started, whereas Androids can be confusing to configure – which mail client do you use? Android is super customizable, but that lack of structure reduces the intuitive grasp of what āshouldā be done. Android helps to mitigate this by layering products on top to provide a more structured environment. With IOS there is innately a rigid structure in place and overtime they have added in customizable features.
There is a tension there, but fundamentally both approaches are an attempt at meeting user experience expectations. A spectrum exists here, and different pieces may require different approaches. The Onping automation platform is probably more towards the Android way of doing things for industrial companies, though we have the capability of providing a more iOS-y out of the box feel.
What are some of the ways you make this Automation Platform easier to use? I know when I get a blank canvas and no rules, itās hard for me to just go. I know there are a lot of things in OnPing that make it easier to use and get past āstartā with the platform. Can you explain how you do that?
Probably the most important thing there is having system templates as starting points. If youāre putting in a new plant or skid design, we have templates to help create an automation environment that feels familiar to you.
Once you get to that first experience that feels nice to you, the fact that you can add what you need and extend it where you want it becomes really important. We have customers that are incredibly data driven, and if you had asked me to pick what their dashboard should look like at first, compared to what it looks like now, I wouldnāt have been close.
We gave them a template, but then they can extend that with widgets and highly interactive design elements that are important to the user.
Especially when you are talking about an automation platform for industrial purposes which, even though Iāve been using the analogy of a phone, is fundamentally different. Youāre trying to make a product, even if itās for internal use, itās still a product that needs to fit the data that you have.
Can you explain where we fit into the broader picture of the automation market?
Well, we may very well be the only industrial automation platform in the market, but there are sets of tools to get to what we are doing. Compared to something like a VT SCADA or Ignition, which is more of a SCADA project, what you have there is a fully featured SCADA product.
However, you miss out on the networking and Cloud-enabled features in OnPing, or at least those features are not as baked in as they are with OnPing. We are Cloud first – we arenāt trying to sell on-premise licenses or anything like that. That sort of Cloud-enabled architecture is where we differ from on-site SCADA.
When you look at hosted-SCADA companies, our edge capabilities enable us to deploy a set of applications out to the field, something you just donāt get from a traditional hosted-SCADA provider. If I need to run scripts over a set of factories, oil wells, or salt-water disposal or water-treatment plants, or if I have a bunch of applications I need to manage, then thatās just not something Iām going to turn to a hosted-SCADA provider to do.
Thatās sort of where the Automation Platform comes in. We are doing a lot more than pulling data and allowing the āwritesā to happen.
So thereās this idea that OnPing exists in a hybrid environment somewhere between āHostedā and āOn-Siteā. The Lumberjack is a big part of that, right?
Oh, absolutely. A lot of companies will have some sort of āEdgeā component out there to pull data, but itās not as integrated into the system as the Lumberjack. We are actually deploying drivers and managing drivers and managing updates, which is a huge difference from that computer just being a gateway for a device.
Our Lumberjack application, which is sort of the core of that, exists on every platform we have. You can pull data without using that edge computer, but that is using OnPing in a really limited way.
Youāve made some distinction in the past between the goals of the OnPing Automation Platform versus AI or machine learning, and something youāve focused on when making that distinction is the human element of the team behind the system. What do you mean by that?
Thatās a tricky question. A lot of what weāre doing is working adjacent to AI and machine learning, especially with analytics folks and forecasting folks. We are trying to put together tools so that your projects can be deployed quickly and tracked optimally.
When Iāve been around people who are trying to do one of these big machine learning projects, I find that thereās sort of this Great Big Goal, then the nitty gritty, and then thereās this gray area in between. And itās tough to see how you get from the nitty gritty up to the Great Big Goal. That is really what I see OnPing allowing people to do.
Letās say you have a plan to figure out which of your factories is the most efficient in your company. Youāll need key metrics to build the model, and meta-metrics to check them, and so starts this complicated process of implementing checks for checks to make sure the model will do what you need it to do. Itās difficult to know how itās going to work out in the end.
Our people really care about that process of getting meaningful data for a rich information ecosystem. Thereās a lot of work in the middle of those invisible layers that goes into getting meaningful bottom line results. The best approach is to focus on clean, well organized information processes.
So often, we talk about the customizability of the OnPing Industrial Automation Platform and, while itās true that it makes for nice visualizations, the secret benefit in the platform is the flexible organization of information at any level, which is incredibly important if you are trying to extract real value out of information.
Thatās a subtle aspect of the platform – itās hard to categorize data. A lot of times, data is uneasily categorized, and sometimes it works now but not later. Human judgement plays a critical role in this process. So itās important to have the flexibility to make those changes when you need them. Part of that is the platform itself – the rest is about having the right people to do the difficult work.
Iād love to get into that a little bit more. The people here really are the ones coming up with the solutions. I know it can get lost in translation when dealing with software. But when a customer calls you up and says, āHey, we have a problem. Can you fix it?ā It really is the team coming together to figure out how to tackle the issue. Can you get into how that process works? And how does that relate to using a platform to automate?
Yeah, so I think the main thing is to listen, to really listen, to what people are saying the problem is, and not spend much time worrying about OnPing at all. The first few meetings should just be about finding what the sketch of a solution would even look like. That can take so many different shapes, but the idea is finding the pain points in whatever process is being automated.
Once you have that, then you can switch gears into trying to solve the problem. A lot of time, that means Iāll go meet with our industrial automation experts, our plc and programming experts, and data scientists that we have in our Plow group, and Iāll ask them how they conceptualize the problem, and what their approaches would be. The key here is they are down-to-earth thinkers. People donāt usually want a science project – they want an answer to the problem in front of them.
Itās ambiguous because itās a process, and changes per client, but itās mostly about listening. Listen to the problem, make a model, listen to feedback, and do that until you find something that you can test out. Then you find something you can test it on.
And that kind of goes back to the Scalability that we discussed before – Iām looking for ways to make the rubber meet the road so we can test out some idea. Once we start testing, we can build the product out and get everyone excited and onboard. The customer is a part of the answer – not just someone waiting for a deliverable – they are a part of the process.
With modern automation projects, thatās the only way to get success. If you keep the stakeholder, the person with the check, uninvolved just calling for updates, they may very well be happy with the product at the end, but itās very unlikely to meet the business needs of the customer. Long term, you need to meet those needs, or youāll just end up being the legacy software in the next build. The next integrator comes in, replaces some stuff, and that just starts a cycle of unwanted software exchanges.
If you solve the problem well, that cycle never gets started, and you never become the legacy software. Youāre just part of the thing that works.
I know when I first started looking into development, I heard the nightmare stories of someone bringing in a website developer, and 6 months in they couldnāt tell you one change that had been made, because they donāt know what is being done. You are taking that opposite approach and really looking at this through a people perspective, and making sure that people are involved and aware of what is happening – almost like people are a key component of automation.
Yeah, it definitely is. One of the things we constantly do when we are starting a new project is try to start at the end of a project. We work back from that to consider the steps it would take to get there. What does it look like when we say weāre done, and what does it take to get there? And what happens when we say weāre done, but now something new has to happen. Because thatās where a well executed project can really come off the rails. If suddenly there are a bunch of changes, then how does the system respond? And those responses are all about buy in. You need to understand who the stakeholders are in the company, you need to understand who the 3rd parties are that may be involved, and make sure that they know how to use whatever system is being developed. Be ready for it to change. Build with the assumption that things will change, donāt assume things will just be there. There are a lot of vague ideas here, because it really just comes down to execution. And we are very good at it. I think a lot of that is because weāve developed a lot of good tools and directions that help keep us grounded and within the rails when we are working.
Youāve mentioned change. One of OnPingās advantages is that it is flexible to change, correct?
Definitely so. Thatās partially because it is Cloud-based software. Anyone that has used Google Chrome or Google Business Suite can see how those products have changed overtime. OnPing has that same sort of feel to it.
The more you use it, the better it feels and the better it responds to what you need. There is no finish line for it. Itās not like, āHere, we’re done. Now you have an OnPing.ā It’s an organically changing thing.
OnPing has changed over the years. You all did not start out as an Industrial Automation Platform. When did you begin to conceptualize OnPing as a solution for Automation at large?
Probably around the time that we realized we were developing applications on edge computers. We started out as a hosted-SCADA platform. We had a vision around that. Weāre happy. There are plenty of people that use OnPing just for that.
But we had a few customers that wanted more. They wanted ticketing applications for saltwater disposals, they wanted the ability to deploy machine learning models, and all kinds of weird and interesting cases that involved people noticing the edge computer we had on site, and asking if we could put something on it.
Instead of just shelling in and adding stuff, we started building those requests into the product directly. That made it so that deployment of those applications was a proper feature in OnPing.
Now everything in OnPing is deployed using the same application engine and thatās made a world of difference for us.
On bringing experience into Automation:
You asked me about the definition of automation earlier. I think anytime youāre dealing with technical systems, once you get over the initial excitement of, āI can make that light switch turn on without touching anything,ā the challenge becomes managing the complexity of the tasks.
And even trying to understand how complex the domain is can be challenging. Thatās something thatās easy to lose. Itās sort of what that grizzled veteran intuition is getting at. There is difficulty involved in these tasks, and these are people that have felt how difficult it is to manage the complexity of these change tasks.
I think the reason I come back to that is because in many peopleās eyes, technology is a young personās game, and manufacturing and industrial equipment is seen as an old personās game. It creates this weird tension as the two worlds are colliding, and I think there are lessons to be learned both ways.
The ways things have been done aren’t always the best ways, but there is hidden complexity in most manufacturing plants that we need to be respectful of. We can often think we know a system but miss something crucial.
That knowledge sounds incredibly valuable.
Personally, I think itās the most important type of knowledge. That sort of tacit understanding of how a particular plant works that a really good operator has is just irreplaceable.
So how do you integrate that knowledge into your industrial automation platform?
Thatās a great question. I think the most successful example of the digitization of that sort of tacit knowledge that I can think of comes from accounting.
There are lots and lots of little accounting rules that business owners and operators have had to deal with over the years. Of course, we live in a world where much of the accounting process has already been digitized so we sort of forget that that world existed and the knowledge simply exists in this digitized form. Thereās still a lot of local knowledge, and that will never change, but itās still digital local knowledge.
Why do I mention that? Well, one of the big keys to that was the invention of the spreadsheet.
Spreadsheets made it where an accountant could move a personal table to a spreadsheet and make some detailed notes to create a rich understanding of some business problem. Understanding business trends and forecasting could now be done quickly with a spreadsheet.
I think a lair like that is what is needed to make the same sort of changes occur on a plant floor. I think the OnPing Industrial Automation Platform is that tool. Thatās one of the things we give you.
We have this really nice engine that allows you to create a new metric and see how it performs relative to intuition. We had this guy that would go out and hit a valve every couple of months because he saw a reading at a certain point.
So it becomes a matter of exactly mimicking what heās doing in a system with a few event scripts so that we can say, āOh, itās hit the valve with a wrench time.ā
Working backwards from what heās doing to whatās happening in the systemā¦. It seems like itās this one very small case, but when you build up all the cases, suddenly you have real business changing automation in a system that wasnāt planned from the beginning, rather built case by case.
Contact Us
Contact us at info@onping.net. Let us know your thoughts on using Automation more effectively in your industry: What common mistakes you have seen? What approaches have worked well in your experience?